
For example, you can change the machine, the tools or the machine head, change the setup settings, adapt the rotation of the axes or even the orientation of the head. The optimisation of CNC programs provides a variety of options to be chosen and defined each time according to the machining conditions. This is because this technology is able to detect possible collisions or more general problems that may arise during the machining.Īll common CNC machines, such as complex multi-axis machines, lathes with live tooling, multitasking machines such as turning-milling units, deep drilling tools and anthropomorphic robots with additional axes, lend themselves perfectly to this type of simulation. With the output from the CNC simulation, the process becomes not only safer, but also more effective and efficient.

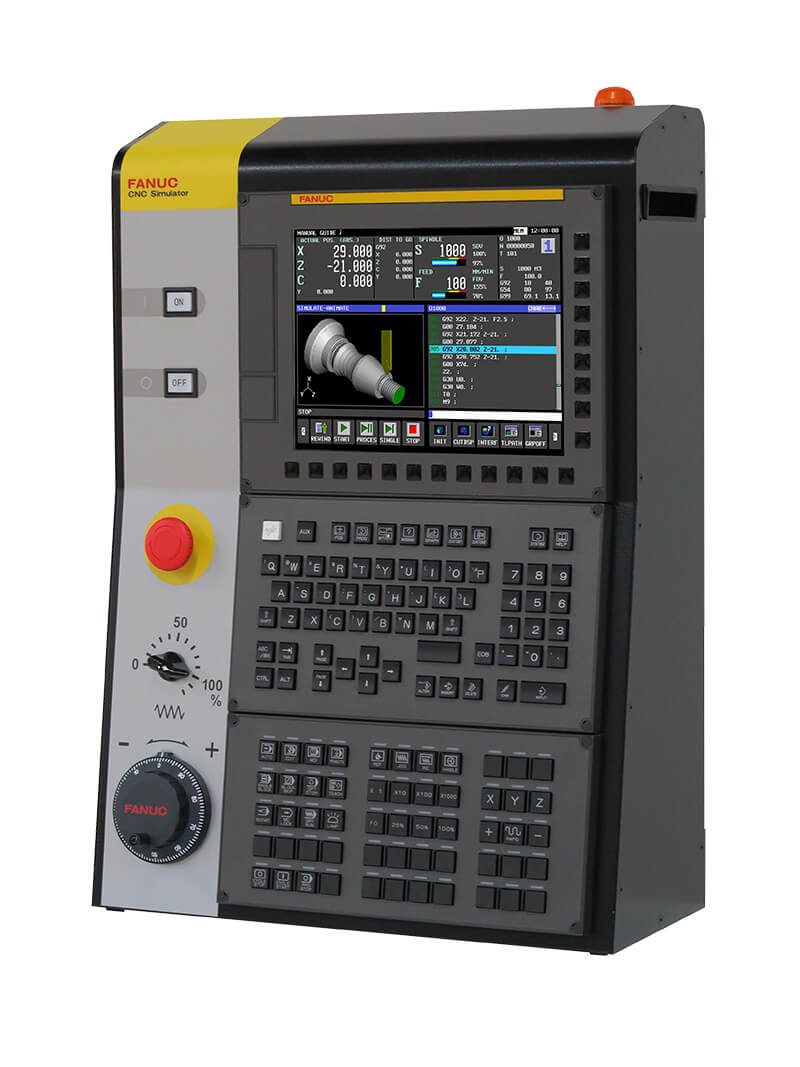
The simulation creates digital copies together with all components. This technology stores all machines, accessories and clamping systems, precisely and on time in the virtual production environment. In other words, you can “ predict the future” of your machining and optimise time, processes and resources.
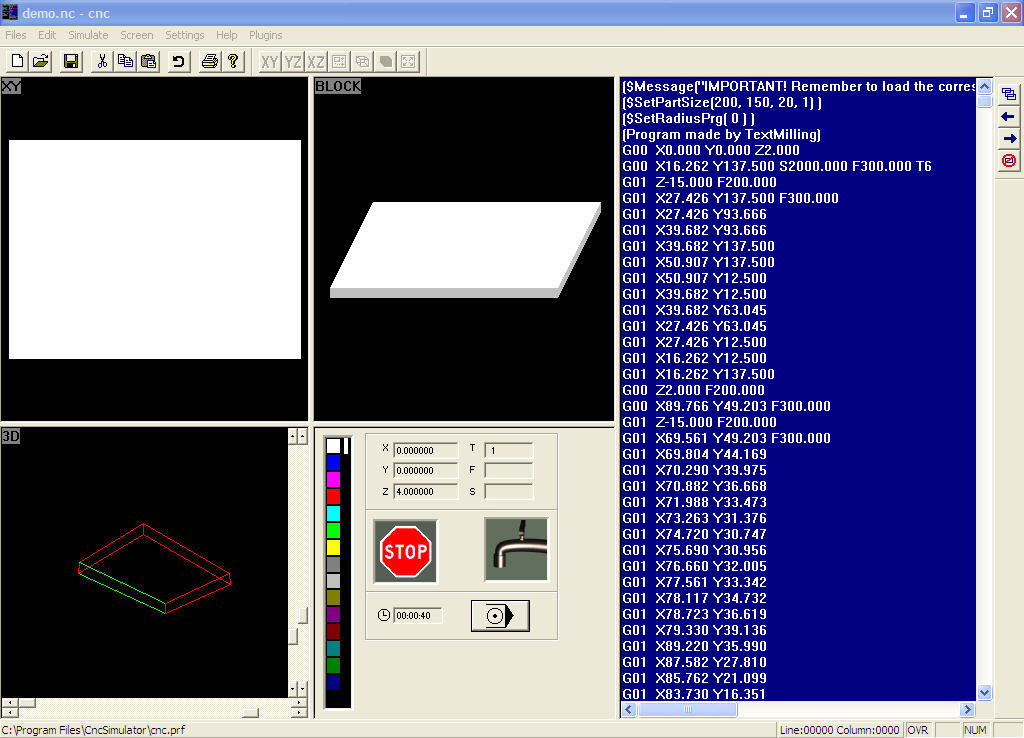
It includes all the components found in the CAD CAM software environment. CNC simulation is an extremely valuable resource because it has the power to plan and verify CNC machining.
